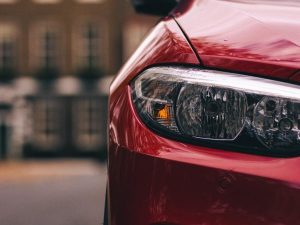
Одной из динамично развивающихся техник производства стеклопластика считается технология вакуумной инфузии. С ее применением выпускают прочные и легкие материалы для многих видов продукции – от небольших кожухов для приборов до крупногабаритных изделий, которые востребованы в судостроении, при тюнинге автомобилей, а также в аэрокосмической отрасли.
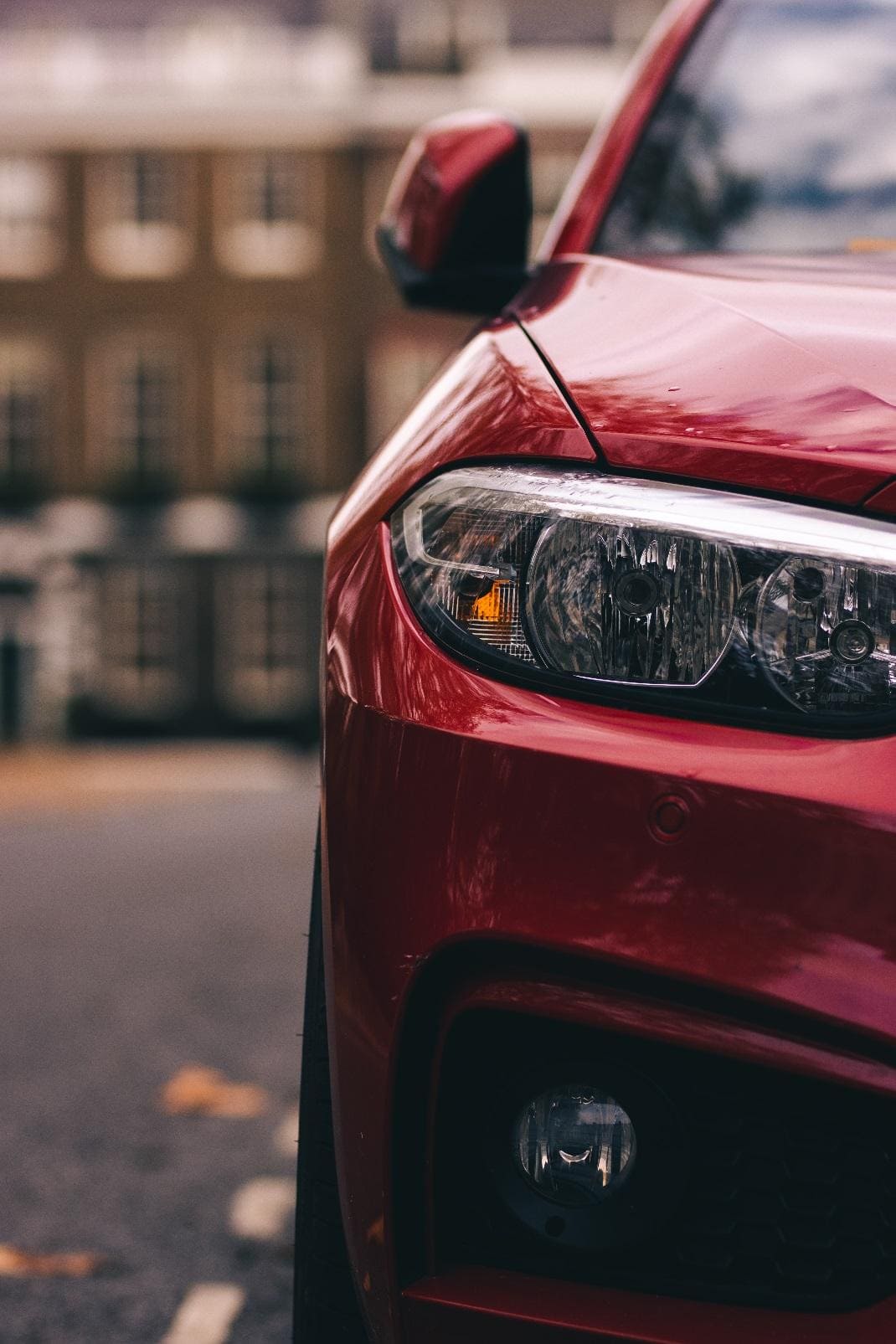
Эта прогрессивная технология имеет существенные отличия от прочих методов производства композитов. В частности, она предъявляет повышенные требования к техническому оснащению, к выбору расходных и вспомогательных материалов. Ключевое значение имеет и то, насколько правильно проходят все стадии при подготовке и в процессе формования будущего изделия.
Общие сведения о технике вакуумной инфузии
Такая технология заключается в пропитывании армирующего материала связующими составами. Само изделие при этом формируется на специально приготовленной болванке или матрице. Есть несколько методик формовки, одной из которых и является рассматриваемая нами вакуумная инфузия.
Свое наименование эта технология получила за то, что для оптимального впитывания (инфузии) связующего состава требуется создание зоны пониженного воздушного давления (вакуума). Поверх рабочей зоны с уложенными в ней слоями армирующего наполнителя монтируют герметичный мешок из специальной пленки, из которого удаляют воздух.
Разрежение позволяет реализовать следующие задачи:
- Запускает поступление связующего состава во внутреннюю часть матрицы.
- Обеспечивает наиболее полное пропитывание материи.
- Способствует надежному прижиманию ткани вакуумной пленкой.
Специфика такой технологии требует соблюдения правил и последовательного выполнения всех стадий техпроцесса. Подробнее рассмотрим каждый этап подготовительных операций и формования изделия, отметим наиболее значимые моменты на каждом этапе.
Тщательная подготовка – залог успеха
При подготовке к формованию стеклопластика по технологии вакуумной инфузии вначале необходимо приготовить все расходные материалы, приспособления и техническое оснащение. Из технических средств основным является вакуумный насос, в сочетании с которым можно задействовать манометр, вакуумное реле, ресивер и регулятор для автоматизированного обеспечения требуемого уровня разрежения.
Для удаления воздуха и поступления смолы в матрицу используют систему трубок, еще один необходимый элемент – ловушка для излишков смолы. Также к оснащению можно отнести матрицу, в точности воспроизводящую очертания и рельеф будущего изделия.
При подборе расходных и сопутствующих материалов следует использовать специальные средства, рассчитанные на нагрузки при низком атмосферном давлении. Использование не предназначенных для этого аналогов может стать причиной нарушения техпроцесса или снижения качества продукции.
Стадии производства
После того как всё техническое оснащение и все необходимые материалы подготовлены, можно приступать к процедуре инфузии. Процесс производства изделия или детали включает в себя несколько ключевых этапов.
Подготовка и проверка матрицы
От тщательности подготовки матрицы зависят итоговое качество, свойства и внешний вид готовой продукции. Ее следует проверить на предмет трещин или отверстий, если есть проблемы – их устраняют.
Материал, из которого сделана матрица, должен обладать устойчивостью к агрессивным средам и к нагреву. При подготовке формы к использованию ее очищают от пыли и загрязнений, после чего на рабочую поверхность наносят воск, поливиниловый спирт или специально подготовленные разделительные составы. Это необходимо для того, чтобы в дальнейшем готовое изделие можно было вынуть из матрицы.
Укладка армирующего материала
В роли армирующего наполнителя применяют угле- и стеклоткани, кевлар, материалы из базальтового волокна и т. д. Вырезанная в соответствии с размерами ткань укладывается в один или в несколько слоев, а для временной ее фиксации могут применяться спрей-клей или качественная липкая лента. Необходимо обеспечить плотное прилегание слоев друг к другу и исключить их смещение в процессе.
Нанесение жертвенной ткани и установка сетки для распределения смолы
Жертвенная ткань помогает исключить повреждение и загрязнение изделия, после затвердевания смолы этот слой снимается. Поверх жертвенного слоя в форму кладут сетку для распределения смолы, которая может быть двух типов – экструдированная или вязаная. Выбор варианта сетки зависит от габаритов изделия, сложности его рельефа и конфигурации, характеристик связующего компонента и целого набора прочих факторов.
Монтаж вакуумного канала и системы подачи полимера
Они выполняются в виде единой системы, по которой удаляют воздух из рабочей области и подают связующий состав. Понижение давления запускает поступление смолы и постепенное пропитывание материала. Вакуумный канал в большинстве случаев размещают по периметру подготовленной формы.
Трубки для подачи связующего полимера располагают в несколько параллельных линий или в виде одного центрального канала с ответвлениями – в зависимости от особенностей производимого изделия. Для перекрытия трубок могут применяться специальные вентили или просто зажимы.
Сборка вакуумного мешка
После того как расходные и вспомогательные материалы уложены в форму, приступают к созданию герметичного пространства внутри матрицы. Для этой цели по краям матрицы с помощью герметизирующего жгута приклеивают многослойную пленку для вакуумирования. Она должна быть таких размеров, чтобы свободно прилегать к изделию по всей площади. Особое внимание следует уделить качеству герметизации, чтобы исключить попадание воздуха во внутреннюю полость.
Проверка герметичности и запуск процесса инфузии
Для тестирования уровня герметичности запускают вакуумный насос без подачи связующего компонента и после откачивания воздуха перекрывают обе трубки (входную и выходную) для проверки стабильности пониженного давления внутри. Если конструкция в течение требуемого времени держит вакуум, начинают пропитывание. По завершении инфузии дожидаются полного схватывания смолы, а потом извлекают готовое изделие для последующей обработки.