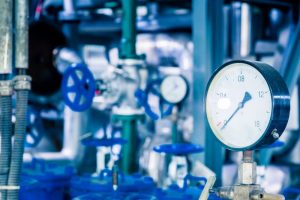
Технология вакуумной инфузии позволяет получить отличные результаты, однако этот метод производства композитных материалов предъявляет высокие требования к техническому оснащению. Так, важно правильно подобрать вакуумный насос, при помощи которого создается пониженное давление в рабочей зоне.
Выбор недостаточно производительного насоса не позволит создать оптимальные условия для протекания процесса. В то же время приобретение насосного оборудования с чрезмерным запасом мощности приводит к нецелесообразному расходованию финансовых средств.
Ниже мы рассмотрим, как и по каким параметрам подбирают вакуумный насос, какие его характеристики наиболее важны, какие факторы учитывают при выборе и какие современные решения применяют при вакуумной инфузии.
Специфика техпроцесса при вакуумной инфузии
Формование будущего изделия из стеклоткани или других аналогичных материалов при вакуумной инфузии происходит с применением специально подготовленной матрицы или болванки – как и при других способах изготовления композитов. Ключевым отличием этого метода является то, что технологический процесс протекает в условиях пониженного атмосферного давления. Именно для создания разрежения в рабочей области и необходим вакуумный насос.
Упрощенно схема технологического процесса в данном случае выглядит так. Над матрицей с уложенными в ней армирующей тканью и слоями вспомогательных материалов формируют вакуумный мешок. Для этого вырезанную по размеру специальную многослойную пленку приклеивают по периметру подготовленной формы при помощи герметизирующего жгута.
В результате при использовании качественных герметизирующих материалов и тщательном выполнении всех работ создается герметичное пространство, из которого через подведенную трубку откачивается воздух. Образование зоны пониженного давления запускает подачу смолы, которая поступает через другую трубочку, подведенную с противоположной стороны.
Таким образом создаются условия для максимально полного пропитывания армирующего наполнителя, исключается вероятность образования пузырьков и непропитанных участков. Кроме того, пленка плотно прижимает армирующий материал к поверхности матрицы, в точности повторяя ее рельеф. Чтобы в процессе вакуумирования разложенные в форме материалы не сместились, их временно фиксируют с применением спрей-клея или качественной липкой ленты.
Характеристики насосного оборудования
Вакуумный насос является ключевым техническим элементом при производстве композитов с применением такой технологии, а правильность его выбора чрезвычайно важна для нормального протекания процесса. Мощности агрегата должно быть достаточно для быстрого откачивания воздуха из герметичной зоны и поддержания требуемого уровня разрежения.
Существует несколько основных технических характеристик вакуумных насосов, по которым можно судить об их эффективности. Так, один из таких параметров – производительность насоса или скорость, с которой устройство откачивает определенный объем воздуха за единицу времени. Этот параметр принято измерять в литрах в минуту (л/мин) или в кубических метрах в час (м3/ч).
Оптимальная производительность насоса зависит от габаритов производимого изделия. Так, при изготовлении детали с площадью порядка одного квадратного метра специалисты в этой отрасли рекомендуют применять насос с производительностью в районе 4–5 м3/ч или до 86 л/мин. Если же происходит формование крупногабаритного изделия с площадью поверхности в 20 квадратных метров, требуется применение насосной установки с производительностью не менее 8–10 м3/ч или до 170 л/мин.
Еще один значимый параметр – предельное остаточное давление, оно характеризуется степенью разрежения, которое насос в состоянии поддерживать в замкнутом объеме. Оптимальной величиной остаточного давления при пропитывании ткани под вакуумом считается показатель в районе 0,01–0,02 МПа в зависимости от размеров будущего изделия и характеристик связующего состава.
Устройство с недостаточной мощностью не обеспечит необходимого отрицательного давления для распространения смолы, а чересчур мощный нерегулируемый аппарат может создать слишком сильное разрежение, при котором смола начнет выделять летучие соединения (закипит), что часто приводит к появлению пористости на готовом изделии.
Факторы выбора насоса для инфузии и различные варианты
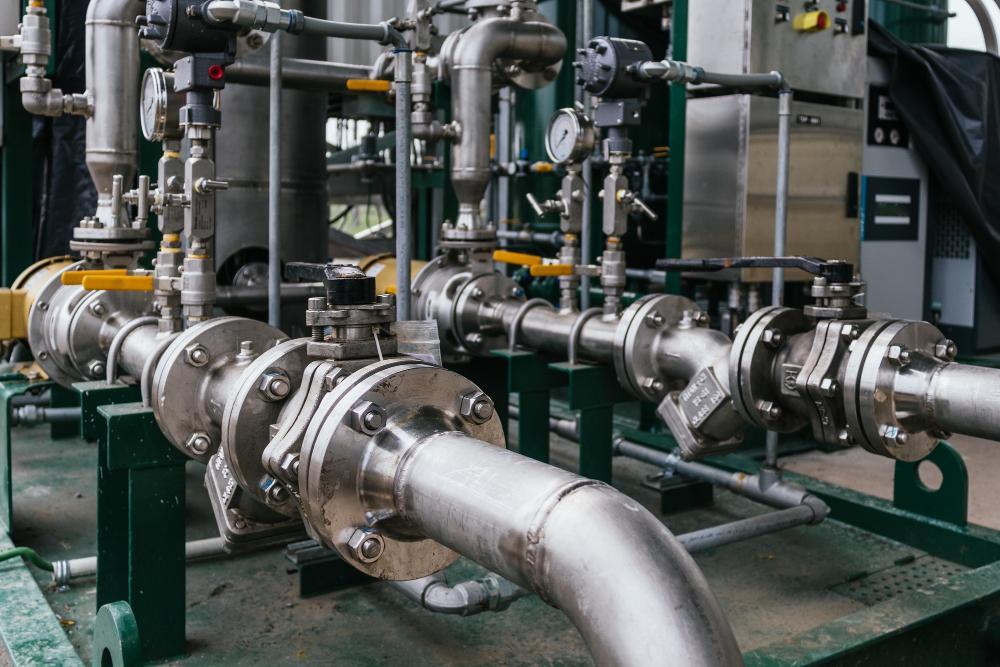
Параметры и тип вакуумного насоса для формования изделий из стеклопластика подбирают в соответствии со спецификой и масштабами производства, характеристиками выпускаемой продукции и другими параметрами.
Так, большое распространение в области формования композитов получили пластинчато-роторные масляные вакуумные насосы. Они достаточно эффективны и экономичны, а их конструкция – надежна и неприхотлива в плане техобслуживания. Среди признанных брендов такого оборудования стоит отметить VARP, Busch, Becker, Leybold, Pneumofore, Edwards.
Устройства этих производителей обеспечивают быстрое откачивание воздуха из герметизированного пространства и высокое качество получаемого вакуума. Их производительность регулируется, а ряд моделей имеют средства автоматизации для стабильного поддержания требуемого уровня разрежения и могут автоматически реагировать на появление протечек.
Существуют и активно применяются комбинированные решения для вакуумной инфузии, в состав которых, помимо насоса, входят и другие контрольные и исполнительные механизмы. Такие станции в зависимости от назначения и специфики использования могут иметь различное исполнение и компоновку:
- В виде передвижного вакуумного поста, смонтированного на тележке, – оптимальное решение для небольшого производства.
- Станция низкого вакуума – стационарно расположенное решение для потребностей среднесерийного производства.
- Станция глубокого вакуума – стационарное решение с большим запасом мощности и производительности для нужд крупносерийного производства.