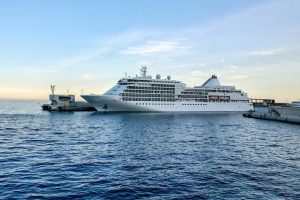
Современные композитные материалы, которые производят по технологии вакуумной инфузии, востребованы во многих отраслях и успешно заменяют собой традиционные решения. Одним из преимуществ такой технологии является возможность производить крупногабаритные изделия, такие как корпуса судов целиком, крылья самолетов, огромные лопасти для ветрогенераторов и многое другое.
Технология вакуумной инфузии является одной из наиболее перспективных среди прочих методик производства композитных материалов. При отличных характеристиках получаемых изделий она экономична и малозатратна, относительно проста по технологии, обеспечивает минимальный контакт работников с вредными компонентами. Поэтому технологи и инженеры стремятся развивать это направление и предлагают новые решения, позволяющие получать всё более впечатляющие результаты.
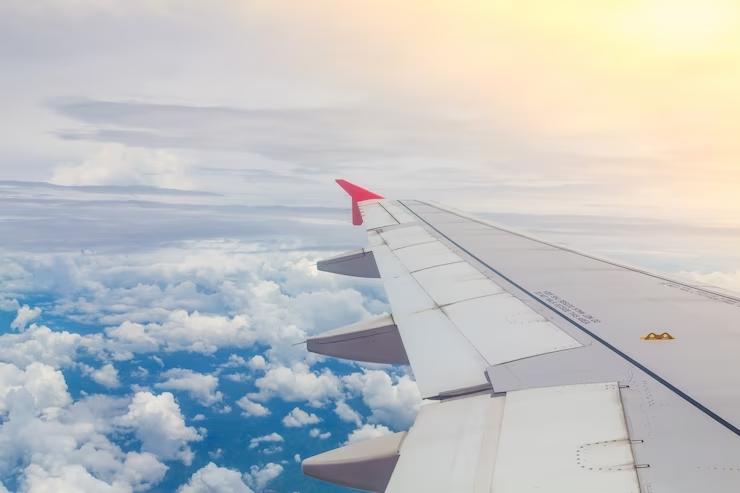
Где востребованы крупногабаритные изделия из композитов
Изготовленные с применением вакуумной инфузии крупногабаритные изделия успешно конкурируют со многими традиционными решениями, при производстве которых применяют такие материалы, как металл или древесина. Особенно активно такое замещение происходит в судостроении и авиастроении – двух отраслях, традиционно довольно консервативных в выборе материалов и технологий.
Так, ряд отечественных разработчиков, в число которых входит и «Курчатовский институт», разработали технологии производства деталей для авиастроительной отрасли. В список предлагаемых и протестированных в различных условиях решений входят как детали для планеров или легкомоторных летательных аппаратов, так и элементы фюзеляжей и крыльев для больших пассажирских или грузовых лайнеров.
Композитное судостроение – тоже одна из растущих отраслей, где востребована технология вакуумной инфузии. В нашей стране эта отрасль представлена несколькими крупными предприятиями (санкт-петербургский Средне-Невский судостроительный завод, ПАО «Амурский судостроительный завод» и другие), которые изготавливают по такой технологии цельные корпуса не только для прогулочных яхт или катеров, но и для военных судов, в частности для минных тральщиков.
В обоих случаях использование вакуумной инфузии позволяет создавать высококачественные крупногабаритные детали экономичным и экологически безопасным способом. Получаемые изделия обладают высокими характеристиками и в состоянии противостоять различным видам нагрузок.
Специфика и преимущества технологии вакуумной инфузии
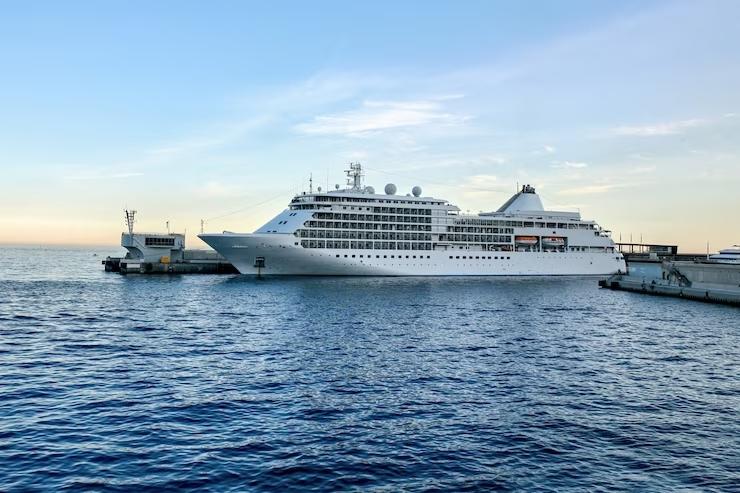
В основе метода вакуумной инфузии лежит разница воздушного давления снаружи и внутри рабочей зоны. Для этого поверх матрицы с уложенными слоями армирующего материала (стеклоткань, углеткань, кевлар или другие материалы) монтируется герметичный мешок из вакуумной пленки. С противоположных сторон к рабочей зоне подводятся трубочки, по одним из которых откачивается воздух, а по другим подается связующий состав (эпоксидная или полиуретановая смола).
Такая технология обеспечивает качественное пропитывание армирующего материала, так как в условиях отсутствия воздуха в рабочей зоне смола полностью заполняет все пустоты. Кроме того, за счет разницы в давлении вакуумная пленка плотно прижимает материал к поверхности матрицы, обеспечивая точное повторение формы и оптимальное соотношение ткани и смолы в получившемся композите.
По сравнению с более традиционным методом контактного формования, при котором все слои материала наносят вручную и прикатывают валиками, при производстве крупногабаритных изделий и деталей вакуумная инфузия обеспечивает целый ряд значимых преимуществ:
- Отсутствие необходимости в ручном формовании изделия и снижение вероятности ошибок или брака.
- Улучшение условий труда сотрудников, которые теперь не контактируют с вредными веществами.
- Многократное сокращение выбросов вредных компонентов в окружающую среду.
- Снижение трудоемкости и общее сокращение продолжительности производственного цикла.
- Повышение качества за счет автоматизированной регулировки распределения смолы.
Требования к организации процесса вакуумной инфузии
При всех преимуществах технологии вакуумной инфузии этот технологический процесс требует тщательного соблюдения условий и применения специализированных высококачественных материалов. Так, для того чтобы впоследствии готовое изделие можно было без проблем вынуть из формы, нужно применять специальные разделительные составы и материалы.
Чтобы ткань пропиталась полностью, связующий компонент должен обладать достаточной степенью текучести и продолжительным временем полимеризации. Чтобы материалы не сместились при подготовке или в процессе инфузии, их фиксируют с помощью спрей-клея или качественной клейкой ленты.
А для надежной герметизации рабочего пространства вакуумную пленку следует приклеивать на тщательно очищенную поверхность и обязательно применять качественный герметизирующий жгут – отлично подойдет для этого двусторонняя клеящая лента Липлент-О на бутилкаучуковой основе.